The machine body adopts the whole steel plate welding structure, tempered by large tempering furnace equipment to eliminate welding stress and deformation caused by machining stress, to ensure that the precision of the machine remains.Imported electro-hydraulic servo valves and scales constitute the precise control mode, with high precision of slider position feedback, accurate and smooth operation, good synchronization performance, bending precision, and high precision of slider repetitive positioning.The hydraulic system adopts integrated control system, which reduces pipeline installation, customer service oil leakage phenomenon, ensures the working stability of the machine tool, and has a simple and beautiful appearance.Mechanical perturbation automatic compensation mechanism, eliminating the influence of slider deformation on the quality of the workpiece, the CNC system automatically adjusts the amount of compensation, easy and accurate operation.
Electro-hydraulic servo numerical control bending machine, the use of mechanical perturbation compensation system to ensure the consistency of the angle of the workpiece after bending molding, the use of servo motors to drive the hydraulic pump, electro-hydraulic servo valves synchronous control, control accuracy, speed, energy saving of 40%, the body of the machine adopts the welding of steel plate, the whole machine by tempering treatment.
Performance Characteristics:
1.Streamlined design, high speed, high precision, high rigidity CNC bending machine, electro-hydraulic servo synchronization technology, more accurate control of the accuracy of the slider.
2.The table mechanical disturbance compensation and throat deformation compensation mechanism, to ensure the bending accuracy, the back stopping material using digital AC servo motor drive, precision ball screw drive, linear guide rail guide.
3.The body of the machine is optimized by finite element design to ensure that the machine is used with high strength and rigidity. Compared with the traditional CNC bending machine, increase the liquid filling flow, oil pump displacement, etc., Y-axis movement frequency than the market mainstream bending machine to enhance about 25%.
4.Adoption of high-frequency resonance proportional valve ensures high stability and accuracy of the machine tool during high-speed operation.
5.Enlarged closure height, throat depth, slide stroke, etc., to facilitate bending and picking up large workpieces and more complex workpieces.
6.Automatic compensation system for mechanical perturbation is equipped as standard, which solves the influence of the deformation generated by the slider in the bending process on the quality of the workpiece conveniently and accurately.
Energy saving bending optimization scheme:
1.High degree of intelligent optimization of bending, very suitable for handling large quantities of complex sizes of the task, in the bending process to provide maximum flexibility and accuracy, in the true sense of the word to achieve time-saving, precision processing of bending workpiece, trouble-free completion of the order task.
2.Bending CNC system has a variety of mold programming (including: free bending, arc bending, depression bending, bending process automatic calculation, etc.) and storage, high-efficiency control algorithms to optimize the machine’s work cycle, the same amount of time can be produced more workpieces, to complete more orders, thereby reducing costs.
3.Ultra-low energy consumption, reduce power consumption than traditional products nearly 60% and low wear and tear.
4.The front feeder device solves the problem of inconvenient bending and carrying of large workpieces.
Standard configuration:
Rigidity strengthening treatment of the frame: the frame components are processed by high-precision large-scale gantry machining centers and automated welding to improve welding uniformity. In addition, the use of vibration aging technology to eliminate residual stress after welding, to ensure the durability and stability of the frame.
Hydraulic system: adopts integrated hydraulic control system, simplifies piping, prevents leakage, improves the stability of the machine tool, and also makes the appearance more simple and beautiful.
Synchronization technology: The cylinder synchronization is controlled by electro-hydraulic servo system, equipped with standard magnetic scale, forming a full closed-loop control, with very high synchronization control accuracy, bending accuracy, repeat positioning accuracy and so on, also reaching a very high level.
Energy-saving system: Saving electricity, servo pump system is on-demand oil supply, greatly improving the energy-saving effect, reducing noise, servo pump system rotates only when needed, noise comprehensively reduced by 30%. Reduce oil temperature, the use of torque limitation and analog speed control, the elimination of valve interception and overflow, greatly reducing the temperature of the oil. Smaller size, simple mounting structure, energy and oil saving, servo motor drive, lower noise, higher efficiency. The cleanliness of the oil has been reduced from NS7 to NS9, and the failure rate of the product is lower. Elimination of proportional valve cutoff and pressure valve overflow, low heat balance temperature, hydraulic oil consumption is reduced by 60% compared with traditional machine tools.
High-precision mechanical compensation device: compensation closed-loop control, high control accuracy, compensation amount is automatically calculated and set by the CNC system to ensure the consistency of the full-length bending angle.
Precision scale: Accurate measurement of the small deformations occurring in the bending force of the machine tool and feedback compensation.
Rear stopping system: imported grinding ball screw drive, linear guide guide, beam double linear guide structure, to ensure accurate positioning. The assembly precision multi-stage blocking finger, increase the positioning range, make bending more convenient.
Precision Quick Clamping Device: It is convenient for quick clamping on the mold, reducing labor intensity and improving production efficiency. It has the advantages of high precision, easy clamping, no loosening, no dropping of tools, etc.
High-quality bending machine molds: forged and processed, quenched as a whole, durable. High precision, high straightness, high repeatability, and finally get the ideal bending effect.
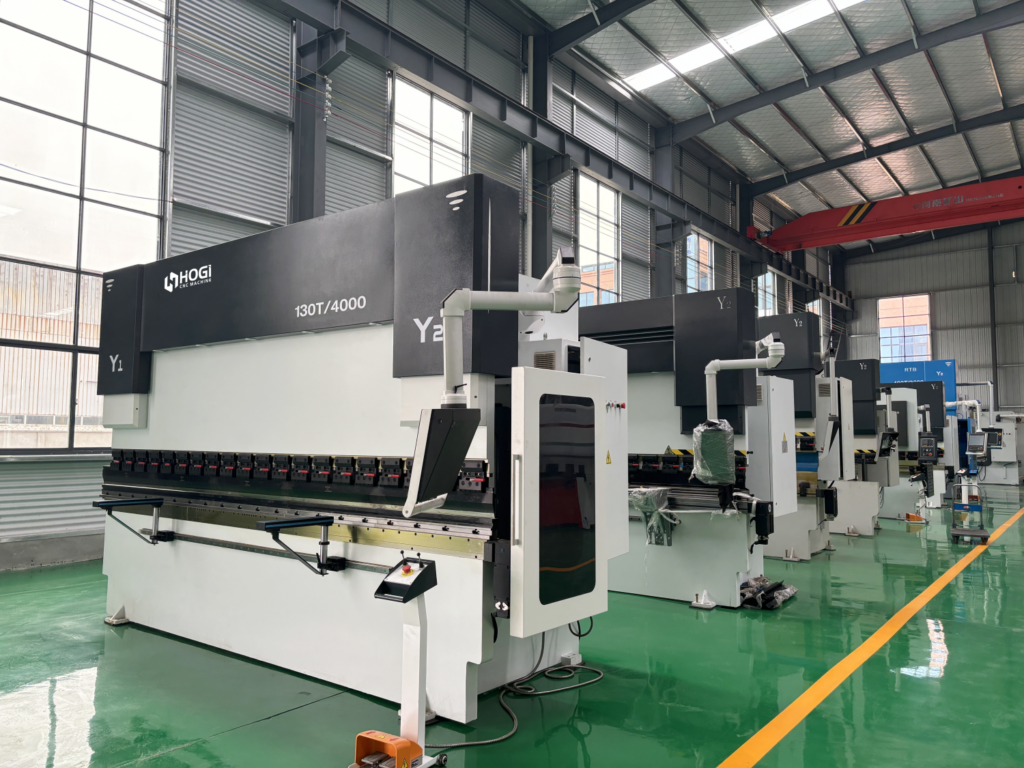